Maintenance plan pays off in six months
Louis Dreyfus biodiesel plant reduces maintenance costs
Instrumentation and maintenance analysis leads to reduced maintenance costs and a fast return on investment.
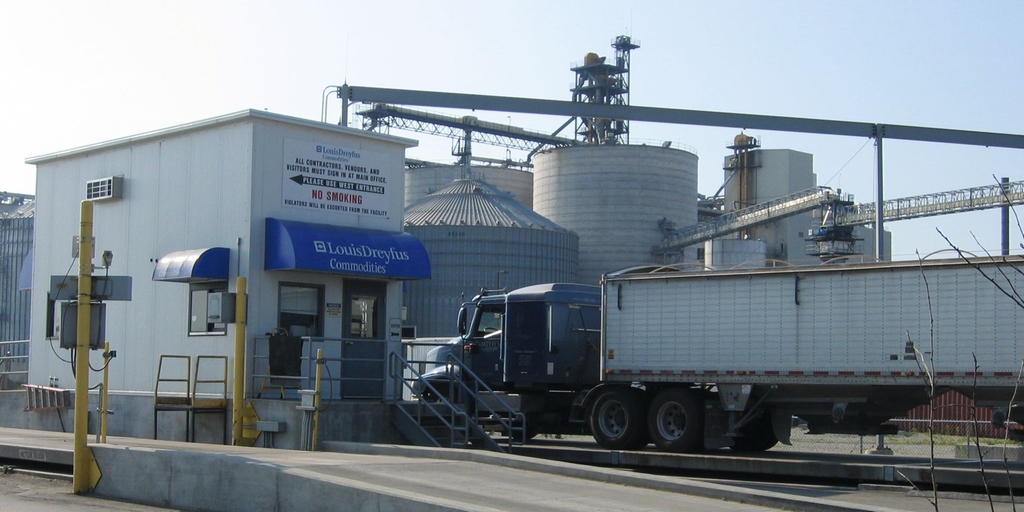
The results
-
Annual maintenance expenses significantly reduced
-
Improved plant efficiency by changing reactive maintenance activities to proactive
-
Developed Predictive/Preventive maintenance plan
-
Established inventory of spare parts for critical instruments
The challenge
The plant manager wanted insight of maintenance activities for budgeting reasons:
Resources were not available nor time to set up effective controls maintenance program
Process efficiency suffered from instrument's reactive maintenance
Our solution
Endress+Hauser performed an Installed Base Analysis which surveyed the plant, analyzed the situation and made recommendations.
Endres+Hauser then developed a maintenance plan, set up a web-based asset information system, trained the customer's personnel and provided all the resources needed to carry out the plan.
The essential steps of the project
Collecting data in the plant
Compiling information and defining critical instruments
Creating maintenance plan
Providing training
Continuous improvement and financial benefits
Annual maintenance expenses have been reduced significantly since the program’s implementation. The plant manager wanted to have insight into maintenance needs for budgeting reasons, but the plant did not have the resources or the time to set up an effective maintenance control plan. Endress+Hauser had the expertise to do so. The plant's maintenance did not have a complete view of all instrumentation information, but the analysis identified 507 instruments with important related information.
Process efficiency, minimized downtime
Previously when an instrument had to be taken out for service for reactive maintenance, uptime was reduced. The resulting maintenance plan helped the customer to anticipate maintenance and helped to better monitor instruments of importance. The plan resulted in scheduled maintenance with improved budgeting costs. Since criticality levels were established, the customer knew which parts needed to be inventoried to decrease plant downtime.